New third-party research proves non-explosive NExP-1 powder performs on budget-friendly printers without compromising quality.
Metal Additive Manufacturing (AM) has transformed how industries approach design and production, but aluminum powders can introduce serious hazards to the workplace—their explosive properties requiring costly safety protocols and expensive storage that restrict their use to specialized facilities.
Facilities operating medium-wattage laser powder bed fusion (L-PBF) machines now have an alternative that offers both safety and performance. Research has validated the non-explosive characteristics of Equispheres NExP-1 aluminum powder and shown that it performs effectively even on more affordable 400W systems—potentially expanding aluminum AM to organizations that previously couldn’t justify the safety infrastructure costs.
Safety challenge in aluminum Additive Manufacturing (AM)
Traditional aluminum powders for AM present serious safety concerns. With particle sizes below 420 μm, they are classified as hazardous substances due to flammability and explosion risks. These characteristics demand specialized storage facilities, handling protocols, and safety equipment—all adding considerable expense to AM operations.
“The explosible character of AlSi10Mg creates a safety risk during handling for operators, implying high safety equipment costs often accompanied by investments in the manufacturing environment,” notes a new research paper from the University of Southern Denmark and Taiyo Nippon Sanso Corporation.
The costly safety and storage protocols surrounding aluminum AM have restricted the use of the technology by many educational institutions, research facilities, and small manufacturers. Beyond the already significant equipment costs, organizations had to invest in specialized infrastructure rather than innovation and contended with concerns for employee and student safety.
AlSi10Mg NExP-1: A safer alternative
Equispheres AlSi10Mg NExP-1 powder represents a significant breakthrough in aluminum AM materials. Through innovative aluminum formulation methods, NExP-1 maintains the desirable AlSi10Mg composition while eliminating explosibility risks.
With NExP-1, we’re fundamentally changing the accessibility equation for aluminum Additive Manufacturing.
The research rigorously validated stated safety claims for NExP-1 through standardized testing and found:
- Lower Explosive Limit (LEL) testing showed no explosion occurred at the test upper limit energy of 300 mJ, compared to explosions experienced at 39 mJ for a traditional AlSi10Mg powder and below 10 mJ for a pure aluminum powder.
- Maximum Explosion Pressure testing resulted in no pressure rise for NExP-1, earning it an st0 classification that certifies its non-explosive nature, compared to 6×10² kPa for traditional AlSi10Mg.
For real-world applications, this breakthrough removes many of the financial and organizational barriers to working with aluminum powders. Educational institutions, small manufacturers, and research labs previously priced out by facility requirements can now enter the aluminum AM space with reduced safety overhead. This research confirms NExP-1 isn’t just a safer powder—it performs exceptionally well on affordable medium-wattage systems, democratizing access to aluminum AM technology that will fuel research and industry advancements.
“Using Equispheres non-explosible powder meant we could print in an otherwise unattainable material family – aluminum alloys” – Andrei-Alexandru Popa
“Using Equispheres non-explosible powder meant we could print in an otherwise unattainable material family – aluminum alloys,” says Andrei-Alexandru Popa, co-author and Associate Professor at the Centre for Industrial Mechanics of the University of Southern Denmark. “This capability opens more possibilities for future research and collaborations while allowing us to expand our commercial activities to a larger array of partners that we previously had to turn down when they requested aluminum 3D printing.”
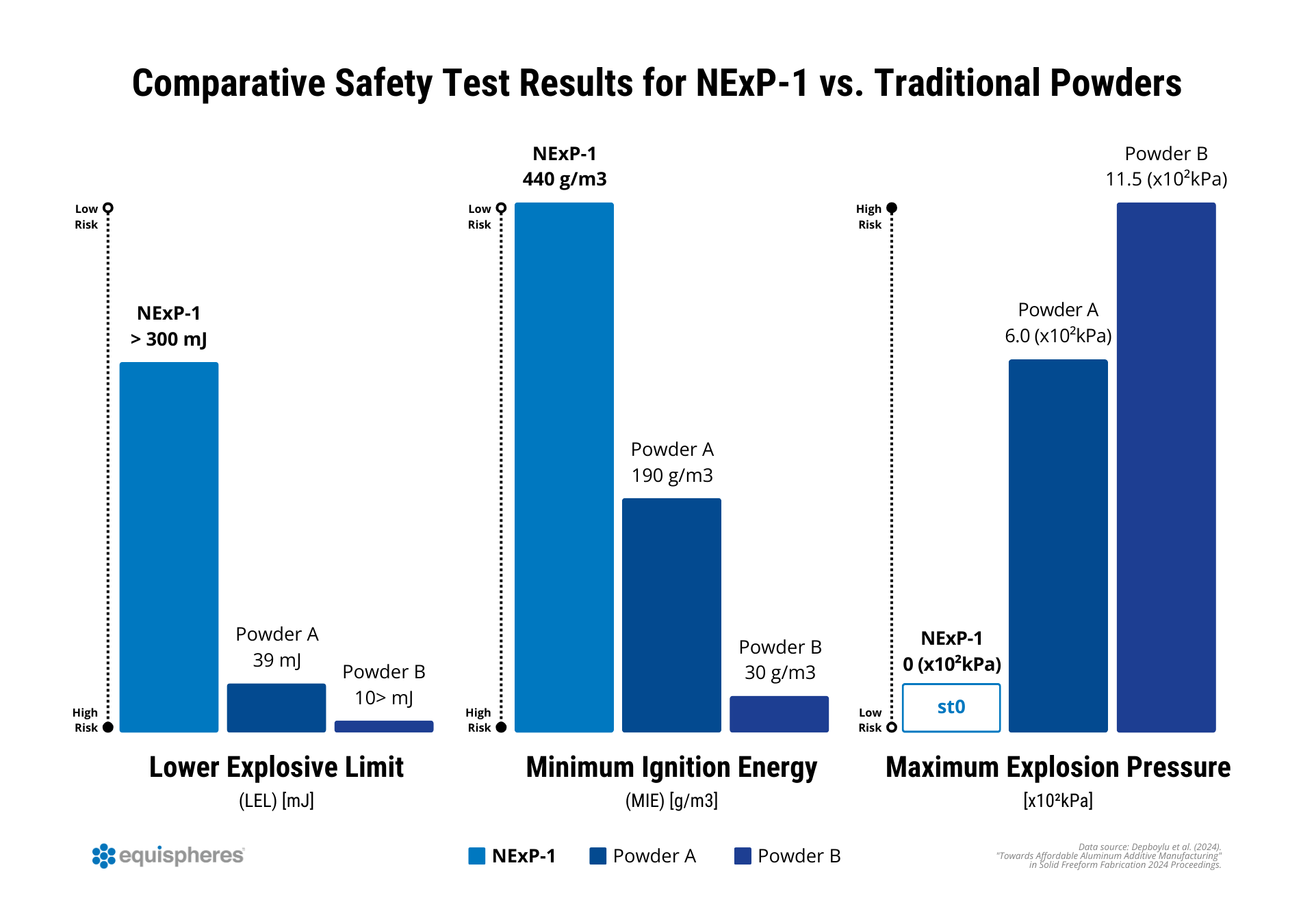
Bridging the gap: NExP-1 on medium-wattage systems
This study pushed the boundaries of NExP-1’s capabilities, testing a powder engineered for industrial-grade 700W+ lasers on the Xact Metal XM200G printer, which features a lower-power 400W laser. The researchers deliberately challenged conventional wisdom, exploring whether this advanced material could deliver performance on affordable systems that would expand access to smaller organizations.
Adapting the use case for lower-wattage systems presents a number of challenges. NExP-1 features uniquely spherical particles with diameters up to just above 100 μm, contrasting with the typical 20-63 μm range typically used on medium-wattage machines. These larger particles can create “atypical energy behavior within the melt pool” when using lower-powered lasers.
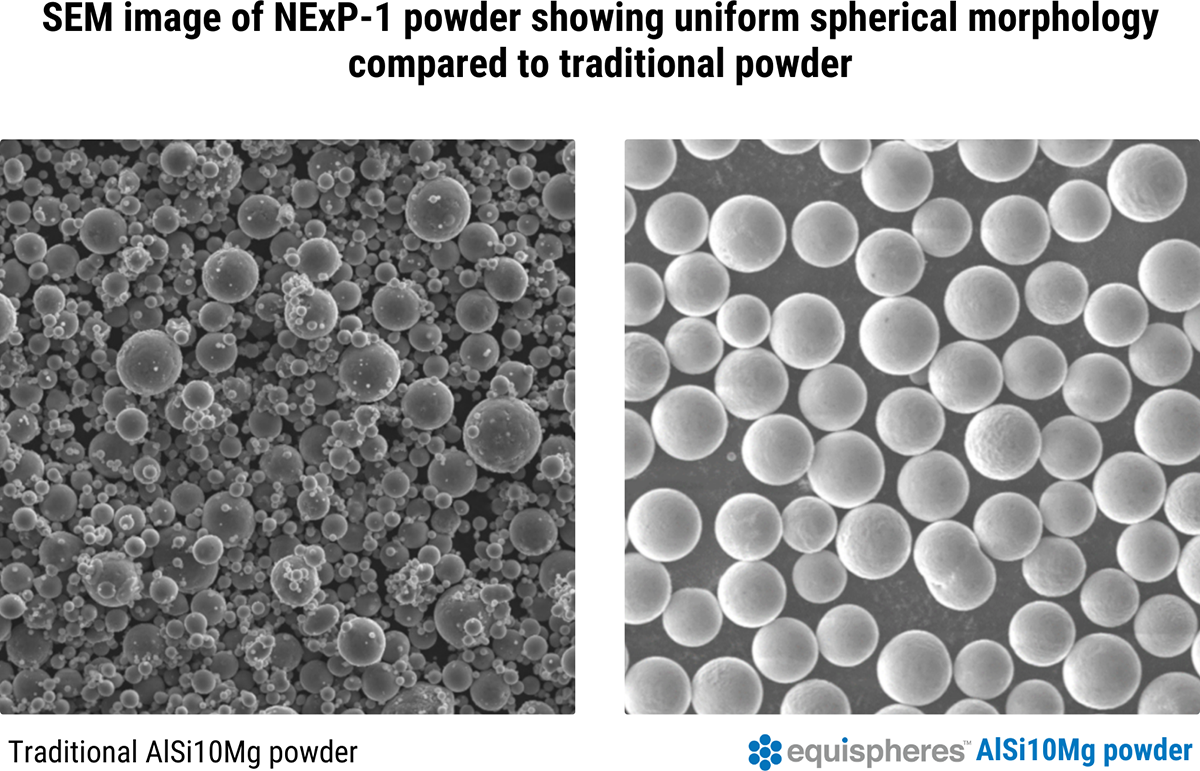
The exceptional sphericity and uniform size of these particles create superior flowability and spreading behavior—properties that enable thicker layers and accelerated build rates on high-powered systems. Harnessing these advantages on medium-wattage equipment, however, requires precision. The researchers faced a delicate challenge: optimizing the interplay between this innovative powder’s unique characteristics and the different energy profile of more affordable printers to produce consistent, repeatable and high-quality aluminum parts.
Process optimization for 400W systems
The research team executed a methodical exploration of processing parameters, designing 16 distinct testing combinations, operating at 390W while maintaining a consistent 60 μm layer thickness. The critical variables under examination were scanning speed and hatch distance, each carefully calibrated to pinpoint optimal performance zones.
Mechanical properties and performance results
Tensile testing on samples produced with the optimal parameters showed promising results. The best-performing parts showed strength values of 355 MPa and elongation of 4.4% when tested. Different printing settings yielded slightly lower strength (316 MPa) and elongation (3.6%). These results match what’s typically expected from this aluminum alloy when processed using standard methods. The parts had a surface smoothness of about 3.85 μm—also comparable to industry standards.
Real-world applications and accessibility
The validation of NExP-1 for medium-wattage systems opens significant opportunities for organizations previously unable to work with aluminum powder in AM processes:
- Educational institutions can incorporate aluminum AM into their curricula without extensive safety modifications to their facilities.
- Research facilities gain a pathway to experiment with aluminum parts while maintaining compatibility with existing equipment.
- Small to medium manufacturers can explore aluminum applications without the prohibitive upfront costs of specialized safety infrastructure.
- Organizations with safety-sensitive environments (e.g., military installations, offshore platforms, or space-constrained facilities) can use aluminum AM with reduced risk.
For these organizations, the economic calculus of aluminum AM has fundamentally shifted. The dual advantage of NExP-1’s performance and dramatically reduced safety overhead— combined with economical print platforms like the Xact Metal XM200G — transforms projects that were previously financial non-starters into viable opportunities. Though the mechanical properties don’t quite reach the gold standard set by high-powered systems, they easily clear the threshold required for many end-use applications, as well as prototyping and functional testing.
“The explosibility results classify NExP-1 as an outstandingly safe feedstock for L-PBF, rendering it very attractive in a manufacturing setup for lightweight applications,” the researchers conclude. “This innovative powder… shows the promising future of non-explosible aluminum-alloy powder for the adoption of affordable additive manufacturing, at no cost to part density or mechanical performance.”
For operations that have long viewed aluminum AM as prohibitive due to added safety requirements, NExP-1 represents nothing less than a transformative opportunity. Organizations can now unlock the potential of aluminum parts production using their existing medium-wattage equipment—without the financial burden of additional specialized safety infrastructure. This accessibility breakthrough doesn’t just incrementally improve the status quo—it fundamentally redefines who can participate in advanced aluminum Additive Manufacturing.
Read the full third-party research paper here: Towards Affordable Aluminum Additive Manufacturing: Considerations on the Manufacturing of Non-Explosible NExP-1 AlSi10Mg on Medium-Wattage Systems
Ready to Embrace More Accessible and Safer Aluminum AM?
Discover how your organization can implement NExP-1 in your existing equipment and production workflow. Our applications engineers can help you determine optimal parameters for your specific printer and applications, providing the guidance needed to achieve exceptional results. Contact us today to schedule a consultation and explore how this revolutionary non-explosible aluminum powder can transform your approach to metal additive manufacturing—without requiring extensive safety infrastructure investments. Let’s work together to unlock the full potential of aluminum AM for your operation.