Originally published on SME.org
The next leap forward in metal additive manufacturing (AM) has arrived in the form of laser beam shaping. The combination of beam shaping and designer metal powders for AM has resulted in remarkable increases in productivity for Laser Powder Bed Fusion (L-PBF) processes.
Applications of metal AM for production parts are growing, but there is still a clear need in the industry for higher throughput if AM is to become an accepted industrial production technology. Beam shaping is being explored by researchers, laser suppliers, equipment manufacturers and materials suppliers as a promising route for the industrialization of metal AM.
When combining beam shaping technology with metal powders designed for printing at high laser power and high scan speeds, L-PBF is seeing a leap forward in production potential.
In L-PBF—also known as direct metal laser sintering (DMLS) and selective laser melting (SLM)—achieving good quality parts at high build rates is limited by the stability of the process. It has been well demonstrated that AM-specific metal powders impart a less chaotic melt pool and are more suited to high-speed processing. In fact, AM-optimized materials are what allowed the industry to successfully use lasers in the 1-kW range to print aluminum parts.
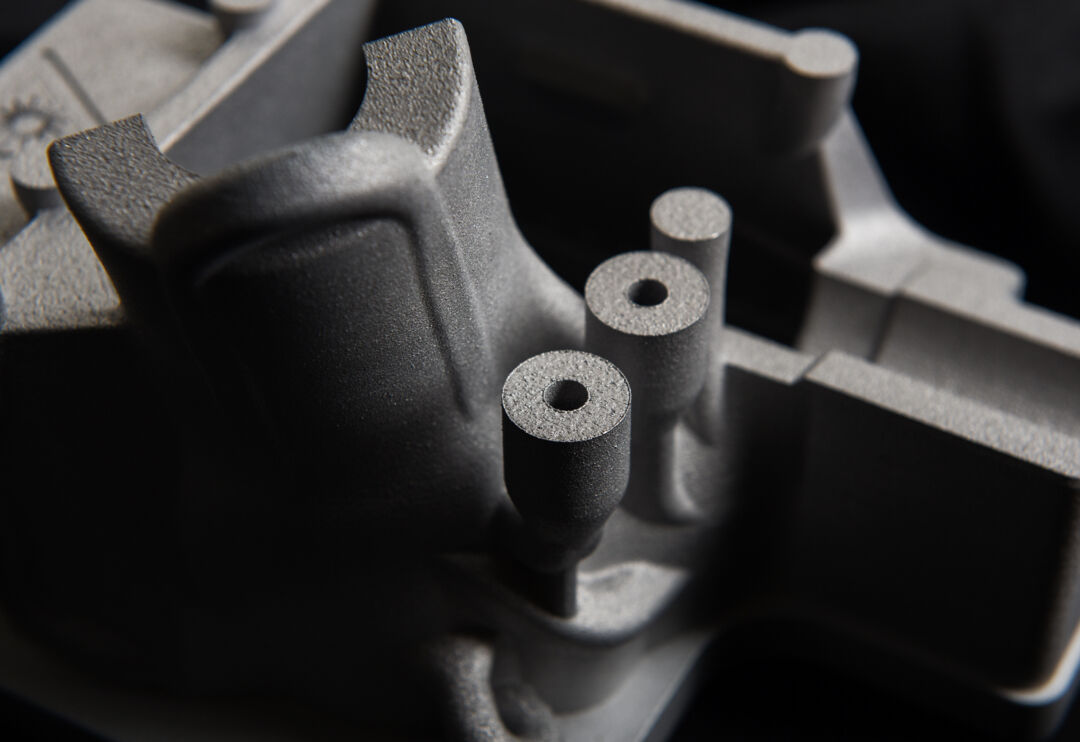
However, producers interested in pushing the boundaries of L-PBF are still hitting limits with the traditional lasers used in the process, as the energy input from these lasers is not ideal for building parts.
This is where laser beam shaping can make a contribution. It is a key innovation that will allow us to capitalize on higher-powered lasers.
How Beam Shaping Boosts Productivity
To understand how modifying the beam shape has an impact on productivity, we need to look closely at how a part is formed during the L-PBF process.
L-PBF machines generally use single-mode lasers with a Gaussian intensity profile (picture a bell curve with more energy in the center and less at the edges). This produces a high peak of temperature in a small area.
When used for bulkier sections of a part, this beam “shape” limits production speed. With energy concentrated down the center of the beam path, achieving quality parts typically requires narrow distances between each track of the laser, increasing the laser time in each layer and increasing build times. When used with higher-powered lasers, this uneven energy input results in more extreme uneven heating and melting that must be corrected. All of this contributes to limiting laser powers in L-PBF machines to roughly 1 kW.
However, by improving beam profiles we can control heat deposition into the workpiece and thus improve how consistently powder is being melted. This means that laser power, scan speed, and therefore build rates, can be increased.
Beam shape directly influences temperature distribution and melt pool characteristics. In a study titled “Laser beam shape optimization in powder bed fusion of metals” researchers noted that ring-shaped and top-hat beam profiles can improve the process efficiency and product quality compared to common Gaussian beam profiles, as they distribute the heat input over a larger area.
Another study, “The influence of novel beam shapes on melt pool shape and mechanical properties of LPBF produced Al-alloy,” found that peak irradiance and the ring intensity had a direct impact on the melt pool aspect ratio and melt pool depth-to-layer thickness ratio.
Similarly, powders engineered for powder bed fusion processes and high processing rates enhance melt pool stability and overall melting behavior. In combination, these two technologies have a powerful beneficial effect on productivity.
How Beam Shaping Reduces Part Costs
From our experience with AM equipment supplier Aconity3D, we know that the material properties are a key factor in taking full advantage of higher-powered lasers.
Equispheres has developed its aluminum powders to suit high-speed processing. It was the specific combination of our engineered powders and 3-kW laser with beam shaping that led to a 9x increase in throughput during our research project with Aconity3D last fall.
One of the drawbacks of laser-based additive processes is the high cost, which is related to low process speeds. Our work with Aconity3D aimed to achieve stable builds with high productivity using high-power lasers (>1 kW) and targeted powder design (meaning particle characteristics are tuned to support high-speed processing). The results remove a barrier to the broader adoption of metal AM, achieving a total per part cost reduction of approximately 80%.
This project demonstrated a sustainable build rate about 9x faster than typical industry production rates. Because so much of the part cost in L-PBF depends on printing time, such a high build rate fundamentally changes the economics of AM processes. The faster process speeds attainable with laser beam shaping, tight process control and next-generation aluminum AM powders will profoundly affect the expansion of AM to cost- and quality-sensitive automotive, aerospace and defense applications.
To permit an accurate determination of time and cost savings, the conditions for this project allowed a direct comparison with earlier research conducted by Equispheres and Aconity3D.
We were able to directly compare the printing time for the same industrial part built with:
- Aconity3D’s standard parameters on a conventional AconityMIDI with traditional aluminum powder (52.6 hours)
- Equispheres’ powder and optimized parameters on a conventional AconityMIDI (17.5 hours)
- Equispheres powder and the AconityMIDI+ outfitted with laser beam shaping and a 3-kW laser (9.5 hours)
The single laser build rate in Scenario C reached 430 cm3/hr and resulted in 80% lower per part costs than Scenario A because of the reduced print time. Our test parts were produced at a layer thickness of 240 μm. Using beam shaping and NExP-1 material, the processing time is only 9.5 hours.
Most aluminum powders cannot handle such high energy input while maintaining a consistent, reliable process. The NExP-1 material used for these trials has unique properties conferred by Equispheres’ powder production process that allow it to support such high laser energy without degrading the process.
Who is Applying Laser Beam Shaping to AM?
Laser beam shaping combined with designer materials allows companies to increase layer thickness, scan speed, hatch distance and energy input. It opens up a world of business opportunities while only requiring modest modifications to process equipment and appropriate material selection.
Within the AM sector, L-PBF systems featuring the nLight laser for dynamic beam shaping are reported to be commercially available from a subsidiary of EOS. Aconity3D has tested a variety of laser configurations on its equipment, including the 3kW laser from IPG used in our collaboration. Civan Lasers also offers dynamic beam shaping and is working with the AM community.
The successful use of a high-powered laser to achieve unheard-of build rates for L-PBF enables a new direction for equipment development. Beam shaping for industrial lasers is already being adopted in other industries and can easily be adapted to L-PBF equipment. Machinery suppliers have an opportunity to adopt this promising technology without affecting the established workflow of L-PBF processes.
The materials technology to maintain a stable melt pool at higher laser power levels is also well-established. Equispheres has numerous clients who are producing aluminum parts at build rates that make metal AM more economical than traditional production methods.
The final step will be the integration of these two technologies, creating more robust business opportunities for additively manufactured aluminum parts by making the process more cost-effective and productive.