Laser beam shaping is poised to shake up metal additive manufacturing. With the combination of beam shaping technology and metal powders designed for printing at high laser power and faster scan speeds, laser powder bed fusion is seeing a leap forward in production potential.
It has been well demonstrated that metal powders designed specifically for additive manufacturing impart a less chaotic melt pool and are more suited to high-speed processing. In fact, AM-optimized materials – like our aluminum powders – are what allowed the industry to successfully use lasers in the 1-kW range to print aluminum parts.
Going forward, producers are interested in pushing the boundaries of L-PBF yet there are production limits with traditional lasers because the energy input from these lasers is not ideal for building parts.
This is where laser beam shaping can make a contribution. It is a key innovation that will allow the industry to capitalize on higher-powered lasers.
Here’s what we have learned since we began exploring laser beam shaping with Aconity3D:
- Our NExP-1 AM powder can handle lasers at least up to 3 kW.
- This high-throughput process works for industrial parts, not just in the lab.
- Beam shaping shows a lot of promise for boosting productivity in metal AM.
Applying laser beam shaping to metal additive manufacturing
Building on an earlier collaboration, Equispheres and Aconity3D explored the effect of “top-hat” and “ring” mode laser profiles on modified Aconity3D machines and Equispheres’ NExP-1 printing material.
We achieved significant productivity improvements in aluminum L-PBF by combining a 3-kW laser, engineered laser beam intensity profiles and our AM-optimized powder. For one part, production speeds over 430 cm3/hr for a single laser were recorded.
We are able to maintain a build-up rate ranging from 6x – 9x faster than typical industry production rates, depending on the build characteristics.
This project shows that specific combinations of equipment and advanced materials can significantly improve productivity for L-PBF, and that we have not reached the limits of this technology.
The process development work performed by Aconity3D and Equispheres differs from previous research in a few ways:
- We used very high-powered lasers.
- We used an engineered aluminum powder with characteristics explicitly tailored to maintain a stable melt pool.
- We used a highly controllable L-PBF machine provided by Aconity3D.
- We specifically targeted requirements for real production parts.
The resulting build rates are beyond anything the industry has seen previously.
Eaton ball valve gets a productivity boost
Having proven the concept for the process, this high-throughput metal AM process developed by Equispheres and Aconity3D was then used to produce a ball valve housing designed by and produced in partnership with Eaton, a world-leading power management company and supplier to the energy, automotive, and aerospace sectors.
The valve housing was manufactured at a single laser build rate about 6x faster than the current industry standard for L-PBF of aluminum while still achieving a density above 99.8%.
The demonstration part is an AM-optimized version of Eaton’s Carter® ball valve housing. The additively manufactured aluminum part was selected by Eaton as an ideal candidate for high-speed AM processing.
There is a clear need in the industry for faster throughput. Because so much of the part cost in L-PBF depends on printing time, such a high build rate fundamentally disrupts the economics of L-PBF processes. These faster process speeds will assist the expansion of AM to the cost- and quality-sensitive automotive, aerospace and defense sectors.
How does high-performance powder increase additive manufacturing throughput?
To understand how the powder-laser combination has an impact on productivity, we need to look closely at how a part is formed during the L-PBF process.
L-PBF machines generally use single-mode lasers with a Gaussian intensity profile (picture a bell curve with more energy in the center and less at the edges). This produces a high peak of temperature in a small area.
When used for bulkier sections of a part, this beam “shape” limits production speed. With energy concentrated down the center of the beam path, it is more difficult to achieve the melt pool characteristics desired for a stable high-speed process. When used with higher-powered lasers, this uneven energy input results in more extreme uneven heating and melting that must be corrected. All of this contributes to limiting laser powers in L-PBF machines to roughly 1 kW.
However, by improving beam profiles, we can control heat deposition into the workpiece and thus improve how consistently powder is being melted. This means that laser power, scan speed and, therefore, build rates can be increased. Enter beam shaping.
The metal powder at the receiving end of this laser energy is critical to making use of such high powers. Most aluminum powders cannot handle the high energy input of more powerful lasers while maintaining a consistent, reliable process. Fortunately, the NExP-1 material used in our collaboration with Aconity3D has unique properties due to Equispheres’ production process and maintains a stable melt pool during printing at very high laser powers and speeds. When the same 430 cm3/hr. process was used to print with a standard aluminum powder used by many production facilities, the relative density of the resulting parts dropped to 98.2% (as compared to 99.8% dense with Equispheres’ NExP-1).
With Equispheres’ production technology, we can tailor powder characteristics, such as microstructure, bulk/surface chemistry, moisture absorption and morphology, to the specific end-use application. We can fine-tune the particle dynamics, like flow and packing density, of our metal powders.
For example, NExP-1 absorbs laser energy evenly and efficiently, which produces a consistent melt pool. Operators are able to spread thicker powder layers and increase scan speeds.
In NExP-1, these powder characteristics are optimized to support the use of high-powered lasers. As a result, the melt pool is much less chaotic than with conventional aluminum powders and high-quality, repeatable parts can be produced more quickly. Our powders drive additive manufacturing efficiency and lower per-part costs by enabling industry-leading print speeds.
The business case for optimized powder and beam shaping
To permit an accurate determination of the time and cost savings generated by this high-throughput process, we produced a part that allowed a direct comparison with earlier research conducted by Equispheres and Aconity3D.
We were able to directly compare the printing time for the same industrial part built with:
- Aconity3D’s standard parameters on a conventional AconityMIDI with traditional aluminum powder = 52.6 hours
- Equispheres’ powder and optimized parameters on a conventional AconityMIDI = 17.5 hours
- Equispheres powder and the AconityMIDI+ outfitted with laser beam shaping and a 3-kW laser = 9.5 hours
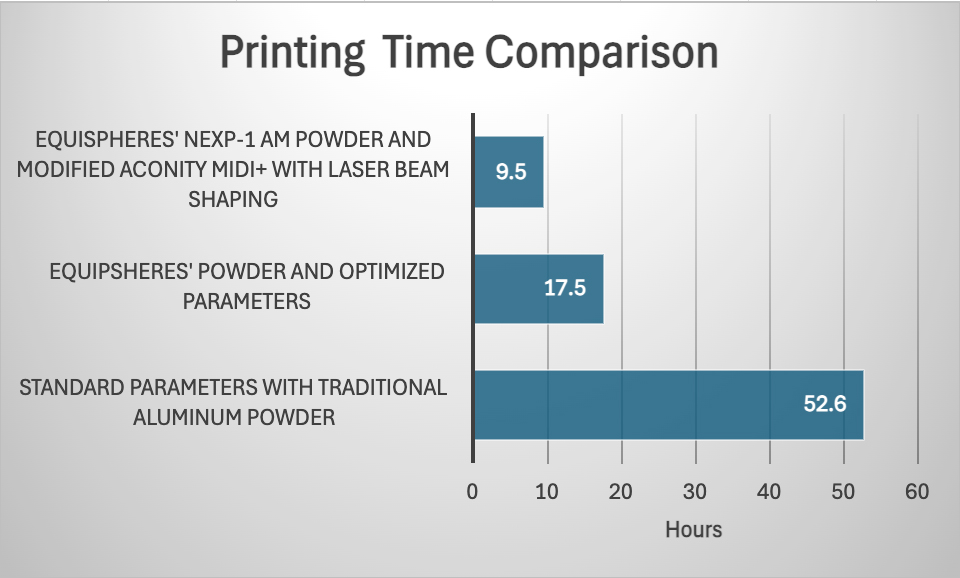
Using this as a benchmark, manufacturers using a similar configuration to Scenario C could expect printing time to be almost 80% less than conventional L-PBF processes and materials.
Our test parts were produced at a layer thickness of 240 μm, achieving a build-up rate of 432 cm3/hr. Using beam shaping and NExP-1 material, the processing time is only 9.5 hours.
For the standard parameter set of 50 μm layer thickness, scan speed of 1350 mm/s and build-up rate of 36.5 cm3/hr., the job time is 52.6 hours. The time savings with the new process is almost 80%.
(For this comparison, some aspects of the job were considered constant: machine preparation took 60 minutes, part extraction took 30 minutes, and inertization and heating took 120 minutes.)
Aluminum is predicted to be the third most popular alloy for metal additive manufacturing by 2030, and currently accounts for approximately 20% of total metal AM materials shipments. Aluminum is on a growth track that will receive a tremendous boost from this higher-speed process.
Who offers laser beam shaping?
Within the additive manufacturing sector, L-PBF systems with laser beam shaping are still a rarity. EOS and nLight have announced a collaboration to make beam shaping and light engine optimization available. Aconity3D has tested a variety of laser configurations on its equipment, including the 3kW laser from IPG used in our collaboration. Civan Lasers also offers dynamic beam shaping and is working with the AM community.
Machinery suppliers have an opportunity to adopt this promising technology without affecting the established workflow of L-PBF processes.
Laser beam shaping, high-powered lasers, and Equispheres’ designer powder is the combo that kicks productivity into high gear.
The materials technology to maintain a stable melt pool at higher laser power levels is also well-established. Equispheres has numerous clients who are producing aluminum parts at build rates that make metal AM more economical than traditional production methods.
The final step will be the integration of these two technologies, creating more robust business opportunities for additively manufactured aluminum parts by making the process more cost-effective and productive.