Heat treating is an often-used and well-understood process in aerospace engineering. When it comes to additively manufactured parts, two challenges cause aerospace companies to approach heat treatment with caution: thermal-induced porosity and distortion.
Neither is insurmountable. As the industry gains a better understanding of the physics and metallurgy involved, we have learned that porosity can be solved by choosing appropriate metal powders.
In recent customer testing, Equispheres aluminum powders demonstrated a significant reduction in the formation of blisters and found that Equispheres aluminum powders significantly reduce the formation of blisters and thermally induced porosity when subjected to T6 heat treatment.
What is thermal-induced porosity?
In discussions with users, it is evident that thermally induced porosity presents challenges during post-processing, such as heat treatment or surface finish. This type of porosity occurs when gas, primarily hydrogen, becomes trapped in the metal during rapid solidification and expands during subsequent heating. The gas is often introduced during the laser melting process, typically due to moisture on the powder surface or hydrogen adsorbed on the surface of the particles.
The common belief that T6 heat treatment is unsuitable for additively manufactured aluminum parts is no longer valid. Parts manufactured with Equispheres engineered powders can undergo heat treatment without experiencing blistering.
Thermally induced porosity is distinct from gas porosity and keyhole pores, though they are related. Gas porosity and keyhole pores form during the laser melting process in Additive Manufacturing (AM), while thermally induced porosity becomes an issue during post-processing, such as solution heat treatments, when trapped gas expands and causes defects.
Hydrogen is a common cause of porosity in aluminum. It has a much higher solubility in liquid aluminum than in solid aluminum. As the metal solidifies, hydrogen becomes trapped, creating pores.
During solution heat treatments, these trapped gases expand and coalesce, leading to thermally induced porosity. This process can enlarge pre-existing pores, resulting in surface blistering, reduced mechanical properties, or increased part volume.
Investigating thermal-induced porosity in AM
Once the industry identified and understood thermal-induced porosity, companies began to modify heat treatment protocols to avoid the high temperatures and long dwell times that can promote pore growth and lead to blistering.
During testing for a customer, we measured and noted porosity in samples before and after typical T6 heat treatment and compared these to data obtained from the literature.
The observations and trends discussed below are based on representative micrographs and are intended for informational purposes only, rather than statistical validity.
For this comparison, we used a solution treatment at 530°C for 6 hours, followed by water quenching and then aged the part at 176°C for 7 hours.
How can we solve porosity to heat treat aluminum?
Altering the heat treatment protocol can be helpful, but it is not 100% effective at eliminating thermal-induced porosity. In our investigations, we found that using Equispheres powder, which adsorbs less moisture, significantly reduces porosity.
Powder characteristics, such as shape and particle size, influence the amount of moisture and gases adsorbed to the surface. Equispheres spherical and consistently sized powder has a lower specific surface area than many other aluminum powders, providing less surface area for hydrogen to nucleate or for moisture to adsorb. This results in reduced moisture and gas content in the liquid melt pool, leading to fewer bubbles in the solidified metal. Once gases are trapped in the metal, thermal-induced porosity becomes a problem in post-processing. The trapped gases form pores, coalesce, and grow when heated at solutioning temperatures.
Figure 1 shows two materials before and after typical T6 heat treatment. There are significantly fewer pores in the Equispheres solidified material on the left. Comparative values can be found in Girelli’s paper in Materials Science and Engineering: A., Volume 739, 2019. This comparison demonstrates that Equispheres engineered powder is atypical when it comes to porosity.
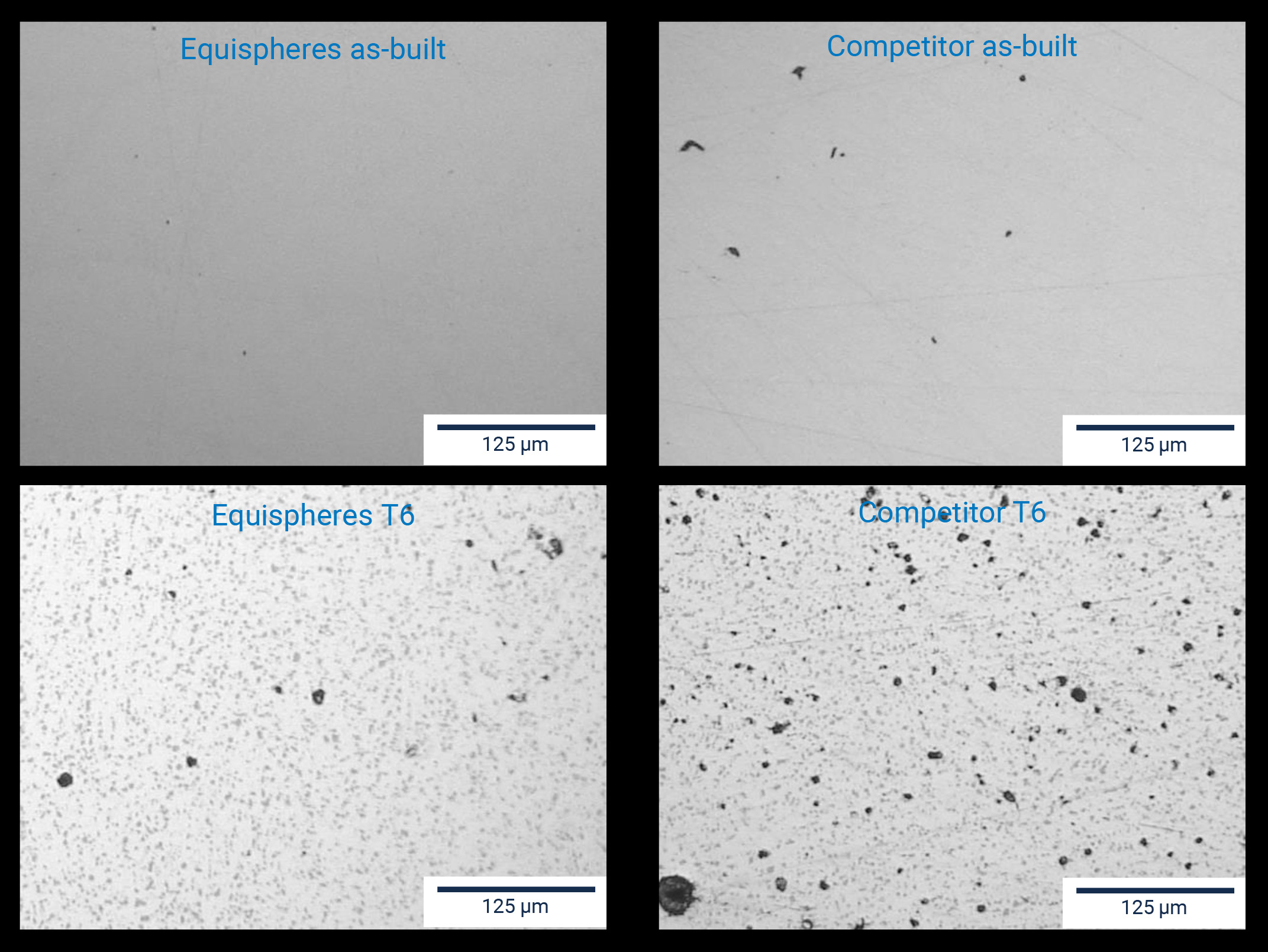
Figure 2 illustrates typical blistering at the edge of the sample for the competitor’s material (lower image). The top image shows Equispheres material treated for 3 hours at 550°C, while the competitor material was treated for only one hour. We extended the treatment time for Equispheres material to monitor the pore growth at temperatures above the typical solution treatment, which help exacerbate the formation of thermal-induced porosity.
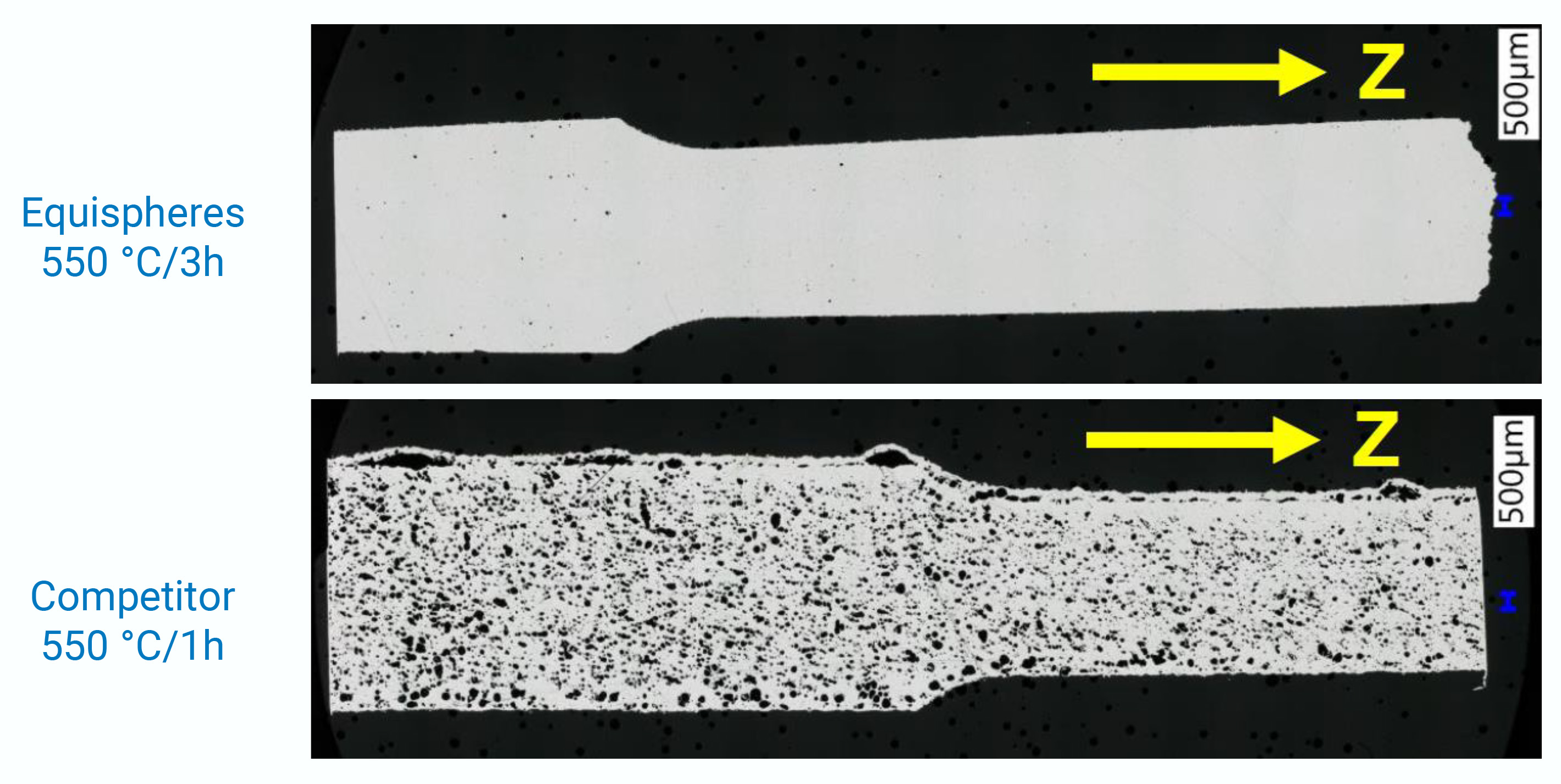
The rule of thumb that T6 heat treatment cannot be applied to additive manufactured aluminum parts is no longer valid. Parts produced with Equispheres engineered powders successfully undergo heat treatment without blistering.
Gaining a deeper understanding of heat treatment for additively manufactured parts and engineering materials is a significant step toward building confidence in AM’s capability to deliver parts that consistently meet industry requirements and safety standards for end-users.