Originally published on SME.org
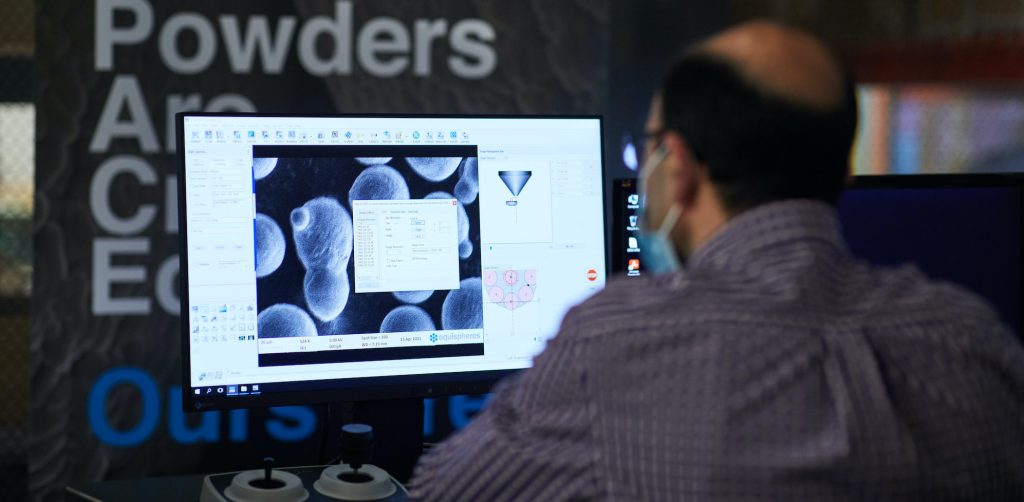
There is a prevailing view within the metal additive manufacturing (AM) sector that innovation in feedstock powders will come primarily in the form of new alloys. While that is certainly a key avenue of exploration, it discounts a major opportunity for innovation related to powder production processes and the ability to tailor the powders themselves to impact AM processes.
Operators know from experience that some powders work better than others, although they may not know why. On the supplier side, it’s common to offer different size classes based on the particle size distribution. But many in the industry don’t realize that material properties that have a direct effect on the bottom line can be tweaked in other ways within existing alloys. This capability will be a defining characteristic of leaders within the AM materials sector for the next decade.
I work with a team of metallurgists who delight in telling me all the amazing things we could do to our AM powders. It’s clear the industry is on the cusp of designer materials, purpose-built powders that provide specific attributes either during the 3D-printing process or in the final part.
Already, metal-powder suppliers are designing materials with properties more suited to next-generation powder bed fusion and binder jetting.
For example, by purposefully engineering toward innovation within the powder manufacturing process, Equispheres has created an aluminum powder that is inherently safer for industrial workplaces. The non-explosible powder was achieved by tailoring the characteristics of a common industry alloy, AlSi10Mg. This was done not by tailoring the chemistry, but the attributes of the individual powder particles.
AM materials are not a commodity product; the material properties matter a great deal. Uncontrolled variations in particle size, shape, and properties result in slower build rates and unreliable parts.
Variability is not acceptable for finished products in aerospace and automotive applications, neither is it acceptable in the source material. Conversely, wise material selection can boost productivity and profitability, make handling and cleanup safer and quicker, and produce more consistent parts.
We have reached a tipping point, and increasing demand for metal AM feedstock will foster more rapid innovation. Wohlers Associates reported that industrywide sales of AM systems for metal parts increased 10.7% in 2021. An estimated 2,397 metal AM machines were sold in 2021, compared to the 2,165 moved in 2020. Revenue from metal grew 23.5% in 2021 to about $473.6 million. The 2022 Wohlers Report also predicted growth in specialized materials for metal 3D printing.
Recent industry growth has brought us to a point where the AM ecosystem and part volumes are accelerating developments that make AM processes better. The combination of new equipment, highly refined processes, and new materials are coming together to accelerate the transition into mainstream applications. Innovating on familiar feedstock to produce designer materials, purpose built to solve problems and open up new frontiers, is also a key step in moving the industry forward.