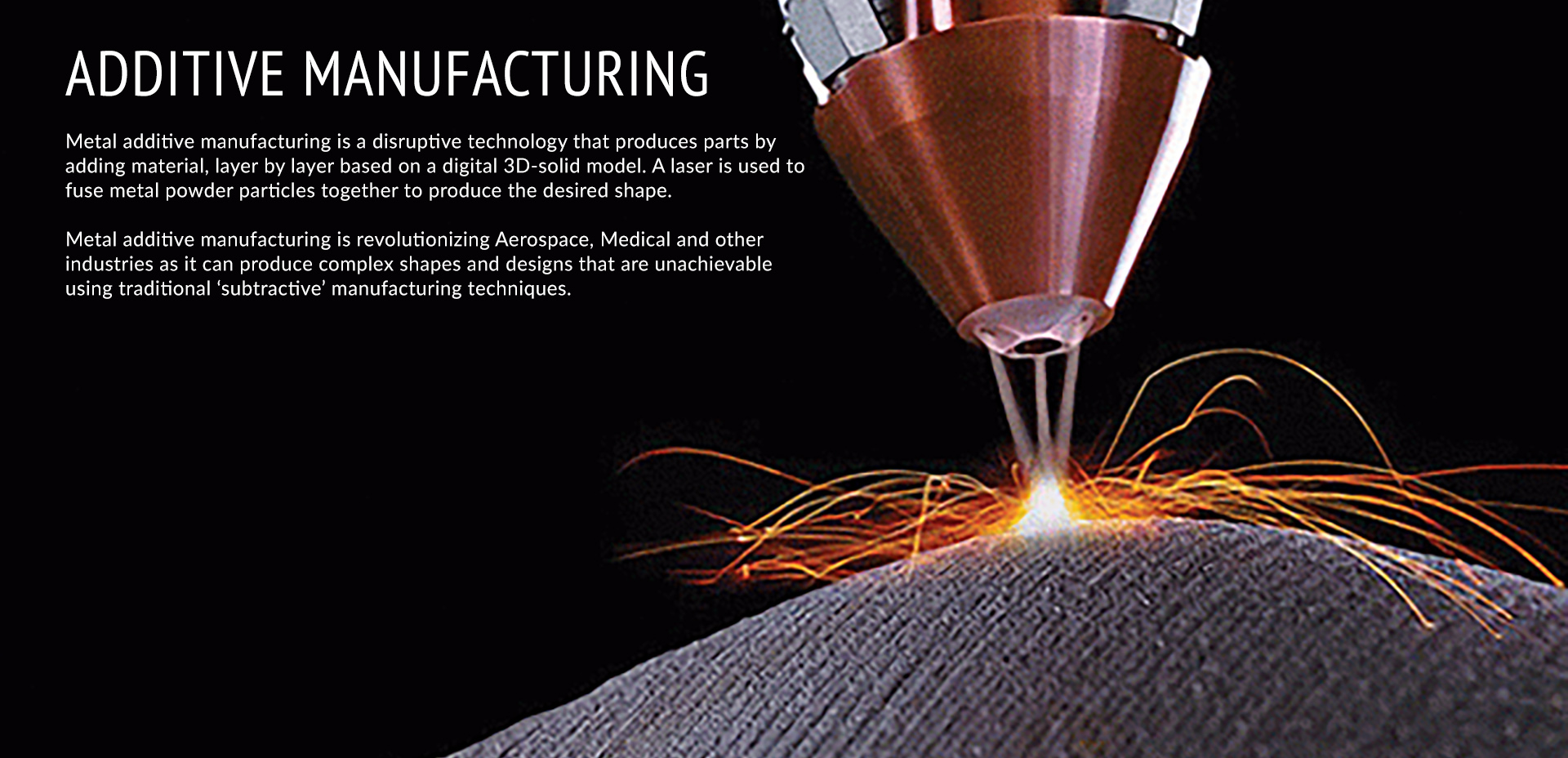
The Importance of Powder to Additive Manufacturing Processes
Based on research and in-field use, the properties of the feedstock powder used in additive manufacturing have a profound impact on the quality of the final product.
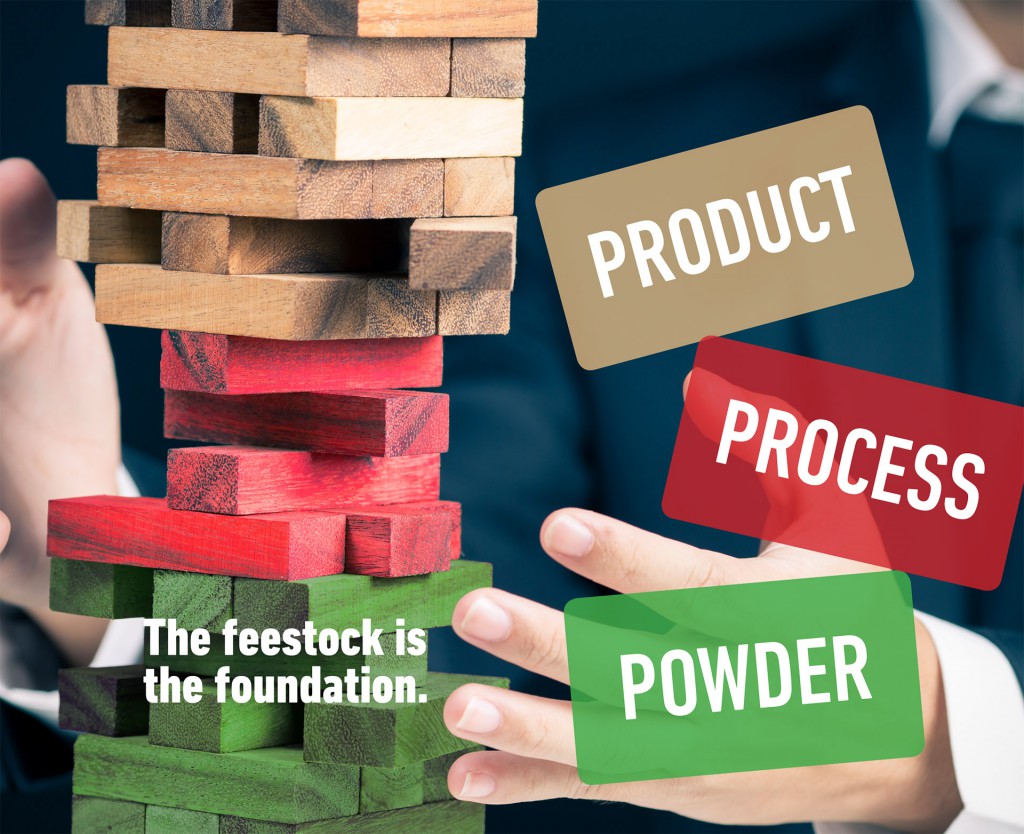
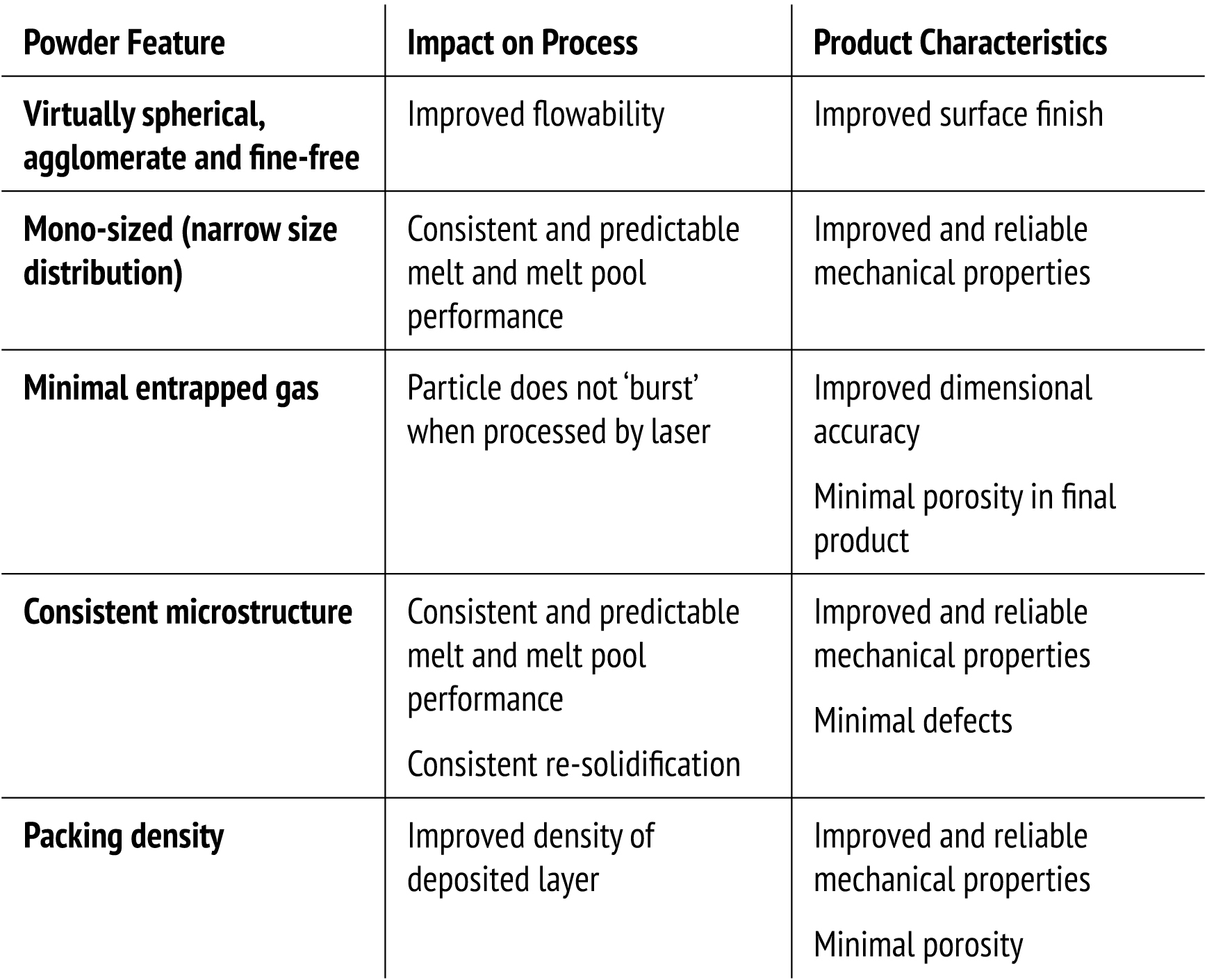

Equispheres
Leading Competitor
Spherical, Agglomerate and Fine–Free with Superior Flowability
Round and smooth particles move more freely than irregular shaped particles with bumps, lumps, bulges and unwanted small ‘fines’ in the way. Said differently, “Particles’ size and size distribution drive powder flowability” [1], and unwanted “fine particles (ø: 0.1-5µm) tend to form clusters and prevent uniform recoating during SLM.” [2]. However, Equispheres’ powder is virtually spherical, agglomerate, fine-free and rolls smoothly under the PBF blade/roller without clumping. Furthermore, research has shown that the “processing of aluminium powders with spherically shaped particles results in the formation of a homogeneous and dense layer” [3]. The result for our customers is a superior surface finish with better mechanical properties in their final product.
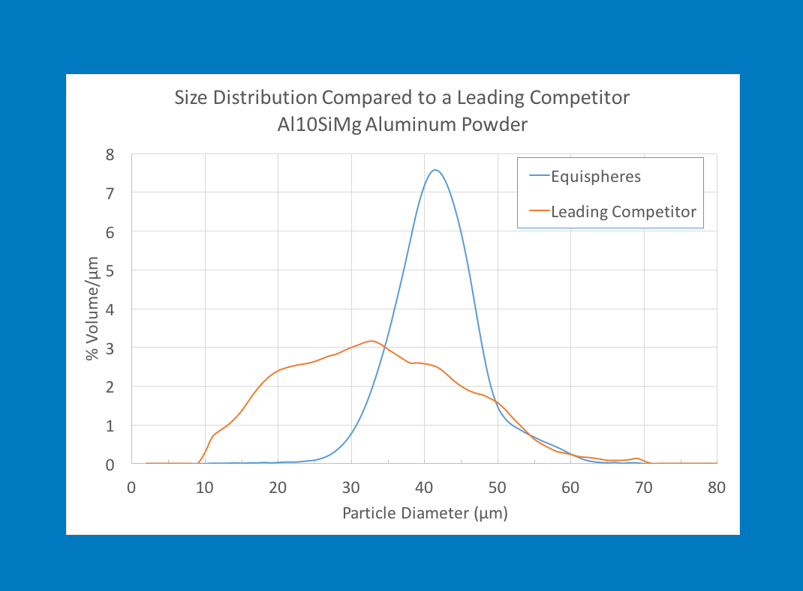
Mono-sized (narrow size distribution)
Smooth round particles that are the same size, naturally arrange themselves consistently for a given volume. Equispheres’ virtually spherical, agglomerate-free powder particles significantly improve the repeatability of the additive manufacturing process because the amount of material for a given volume is uniform and the quantity of material to be heated by the incoming energy pulse is consistent. Thus, the temperature, the melting, and the solidification speed in the affected volume is constant which results in a chemically homogenous deposition layer. Ultimately, this provides superior and consistent mechanical properties in the final product.
Consistent Microstructure
The Equispheres novel atomization process is highly controlled and brings a very consistent thermal history during solidification. Because our particles are spherical and mono-sized, the cooling and solidification process is consistent across all particles. This is in stark contrast to traditional processes involving particles of various sizes whereby by the smaller particles cool faster and produce a much finer microstructure than the neighboring larger particles. The consistent microstructure of the Equispheres powder melts and solidifies uniformly and predictably. The result for our customers is a final product with consistent and superior mechanical properties.
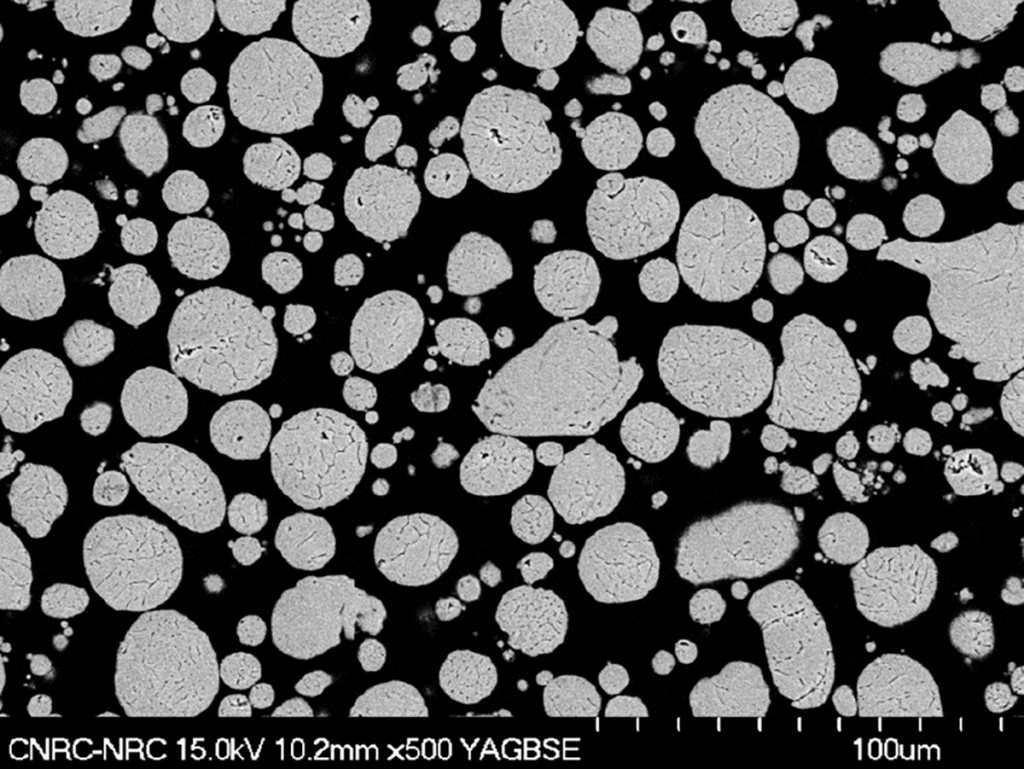
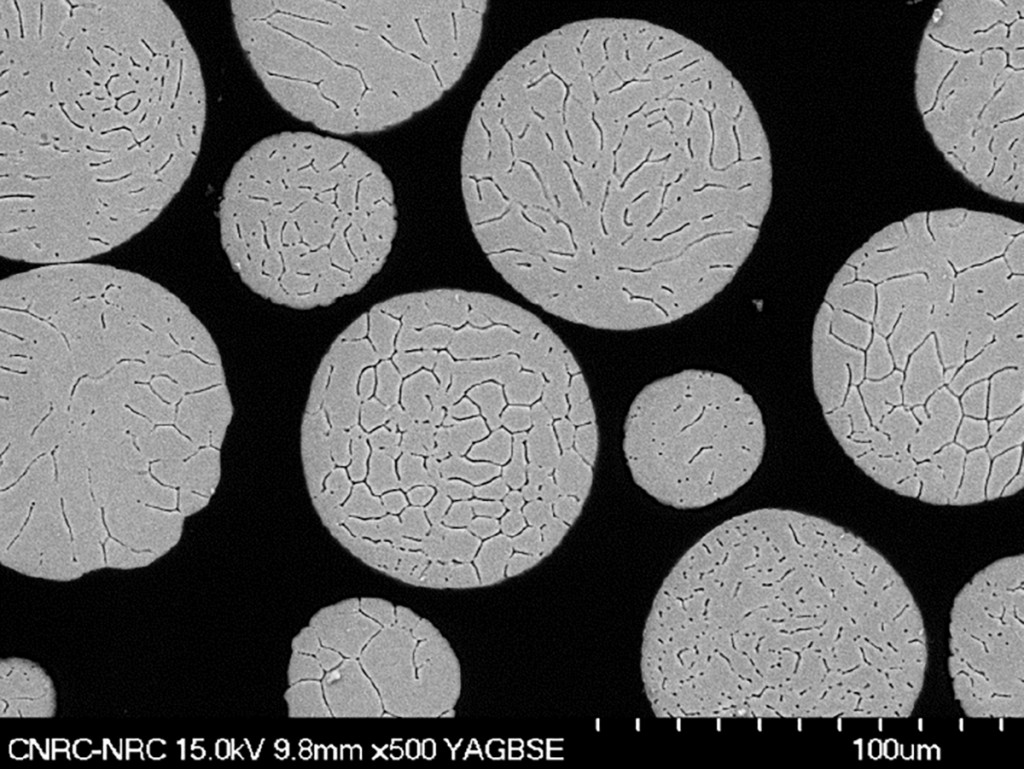
Cross section of leading competitor aluminum – visible entrapped gas
Cross section of Equispheres’ aluminium – consistent microstructure with no entrapped gas
Packing Density
Unwanted agglomerates, ‘potato-shape’ particles and meddlesome ‘fines’ get in the way when powder particles settle in a powder-bed. This has a significant and negative impact on packing density. Because Equispheres’ powder is virtually spherical, mono-sized, agglomerate and fine-free, the powder packs much better than leading competitors. In fact, using the ASTMB 212-99 Apparent Density assessment, the powder packs 30% better. Packing density is important in that “a higher powder packing density produces dense(r) parts with smoother as-built surfaces.” [4, 5]
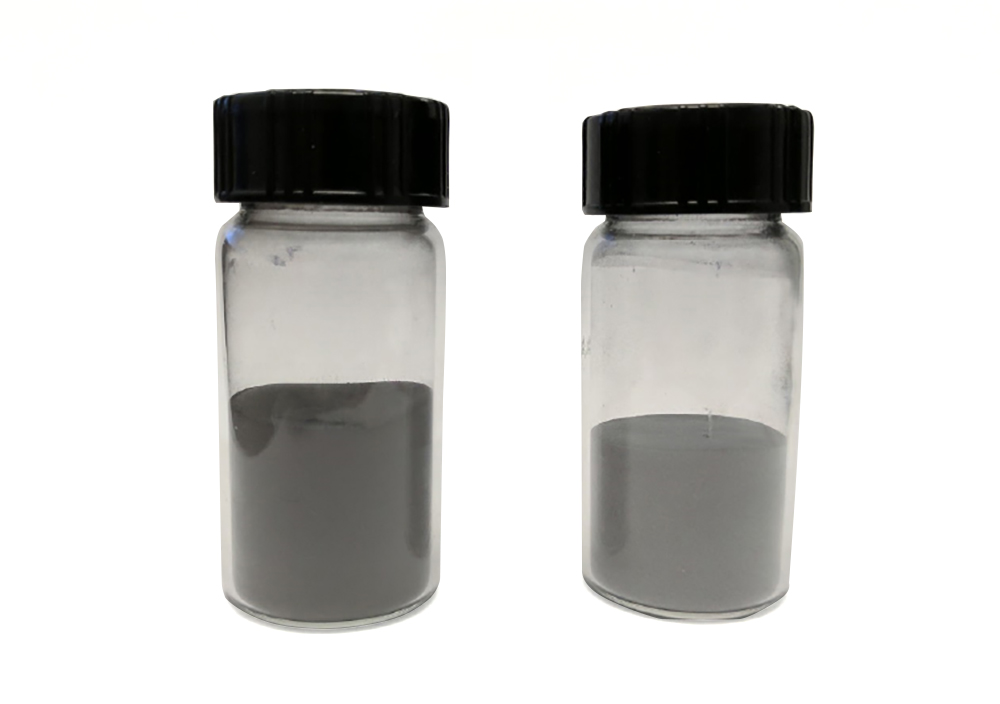
Competitor’s Powder Equispheres’ Powder
Equispheres is presently working with leading academic and research organizations to verify and quantify the impact of the key powder features discussed above.
[1] – Inside Metal Manufacturing – The role of (super) powder in SLM 04/10/2014
[2] – R. K. Mcgeary, “Mechanical Packing,” J. Am. Ceram. Soc., vol. 58, no. 1931, 1955.
[3] E. O. Olakanmi, “Selective laser sintering/melting (SLS/SLM) of pure Al, Al–Mg, and Al–Si powders: Effect of processing conditions and powder properties,” J. Mater. Process. Technol., vol. 213, no. 8, pp. 1387–1405, Aug. 2013.
[4] Korner C, Bauereiss A, Attar E (2013) Fundamental consolidation mechanisms during selective beam melting of powders. Model Simul Mater Sci Eng 21(8):085011
[5] Spierings A, Herres N, Levy G (2011) Influence of the particle size distribution on surface quality and mechanical properties in am steel parts. Rapid Prototyping J 17(3):195-202