Production cost cut by 50%
Breakthrough speeds and cost reductions in aluminum part production have been achieved using Equispheres’ aluminum powder. Aconity3D was able to reduce printing time by more than 60% when printing a complex equipment component with Equispheres’ Performance AlSi10Mg powder. The faster print time contributes to a 50% decrease in part cost.
The increased productivity is achieved by a holistic approach, optimizing material, machine, process and part design.
Highlights:
- Print 3x faster
- 53-hour build time drops to 17.5 hours
- Reduce part cost by 50%
- Complex part with integrated water and air channels
Industry Challenge
For most traditional aluminum powders, inconsistent material characteristics mean the material must be processed slowly on Selective Laser Melting printers to achieve reliable properties in the finished part. Manufacturers must compromise between build speed and part consistency.
Metal powders made using traditional atomization methods cannot deliver the consistency required for higher speed processing on modern, high-powered powder bed fusion equipment.
Equispheres’ monodisperse, uniform, spherical powder absorbs laser energy uniformly. This creates a stable melt pool that allows manufacturers to increase laser scan speed and hatch distance.
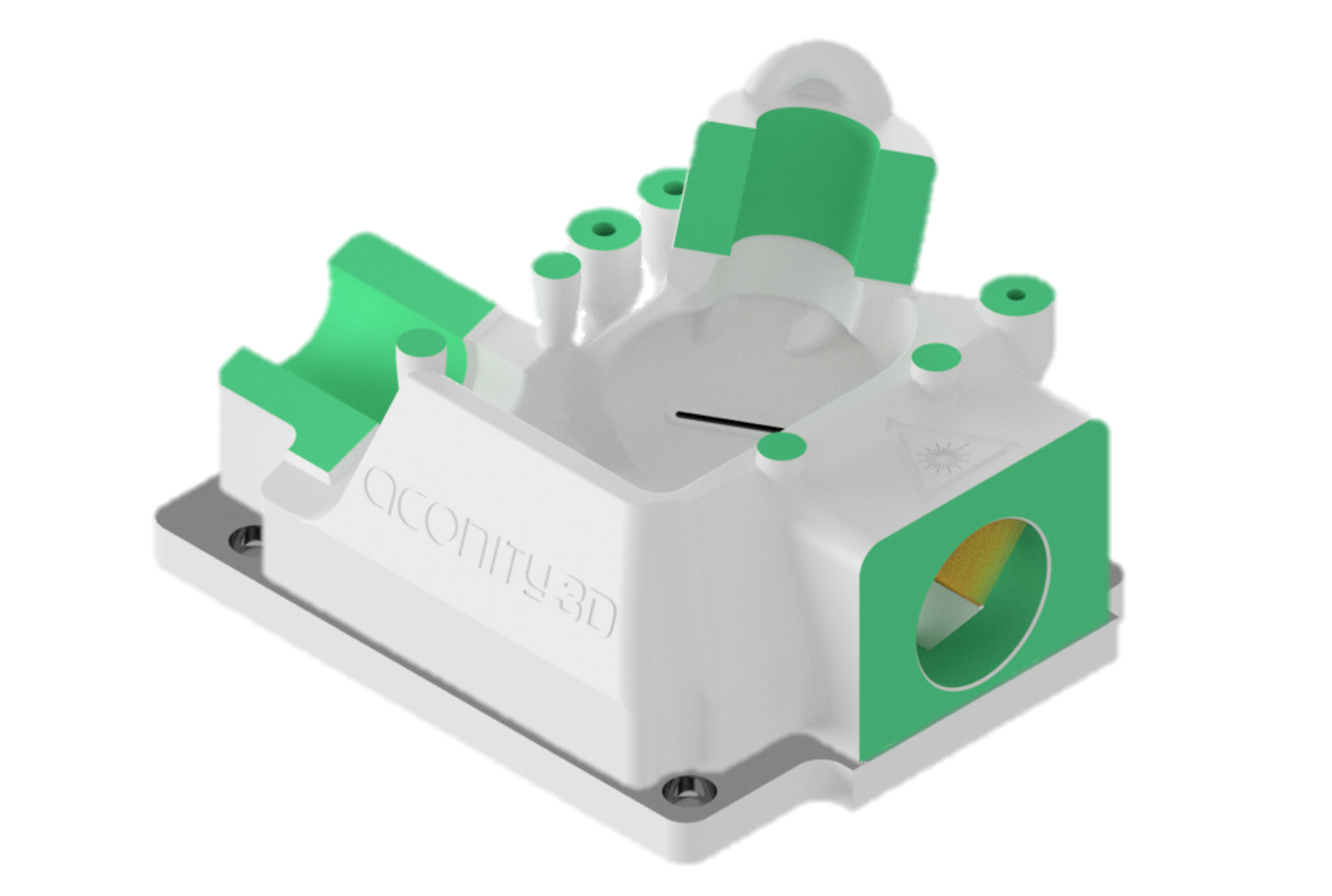
What was discovered
Aconity3D is a manufacturer of additive manufacturing printers. The company used Equispheres’ powder to print a complex scan head used in its line of printers, with the aim of producing the part more quickly and at a lower cost than is achievable with standard powder.
Aconity3D confirmed its part can be produced 3x faster using Equispheres’ high-performance powder with no impact on part functionality. Using the AconityTWO powder bed fusion machine, the company was able to reduce printing time from 53 hours with standard material to 17.5 hours.
The highly spherical and uniform Equispheres powder allows manufacturers to take full advantage of modern, powerful lasers in a way that standard aluminum powders cannot.
Key results
Outstanding powder quality allows high-power processing
Equispheres’ high-performance AlSi10Mg powder provides high flowability, less evaporation, higher powder deposition speeds and stable melt pool formation. For Aconity3D’s 1-kw printer, these powder characteristics permit thicker layers (120 µm) and faster scan speeds (2200 mm/s), resulting in a build rate of 152 cm3/h. Highest production build rate in the market.
Highest production build rate in the market
A direct comparison between the standard feedstock previously used by Aconity3D for this part and Equispheres’ powder illustrates the dramatic increase in productivity.
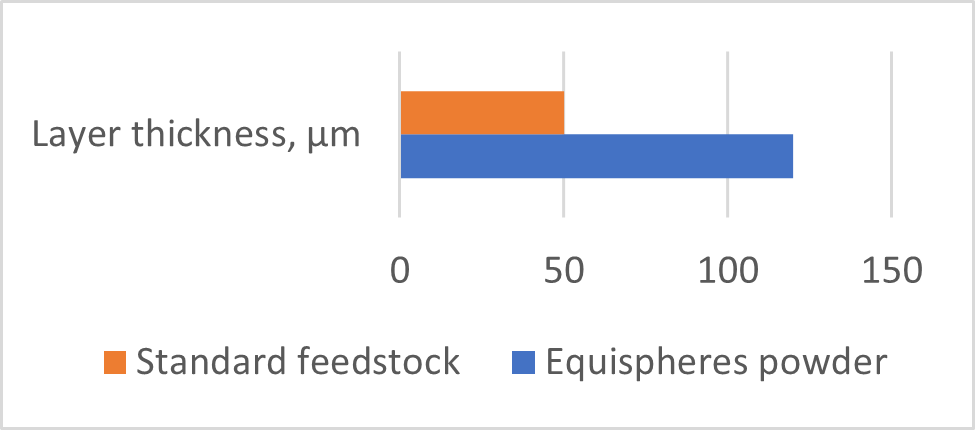
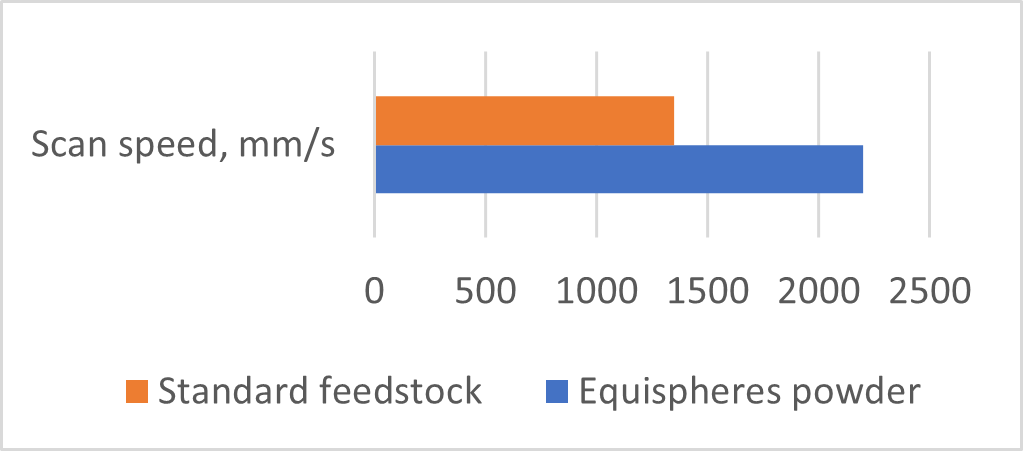
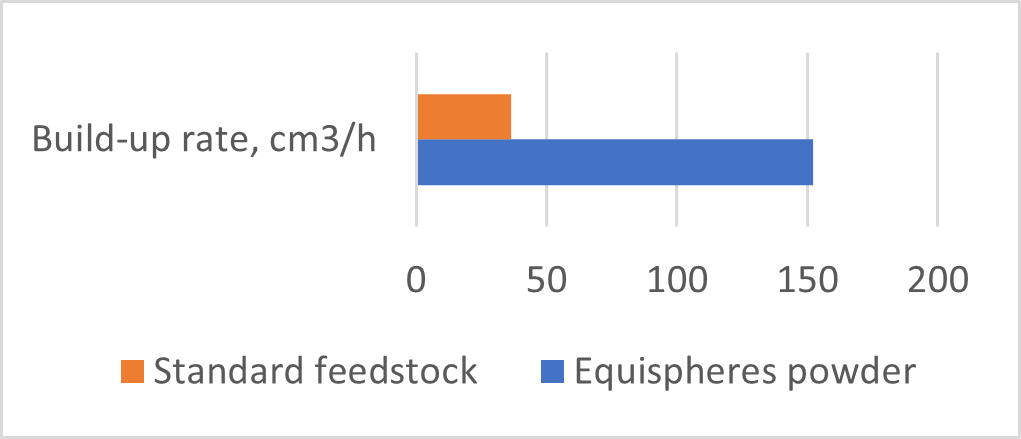
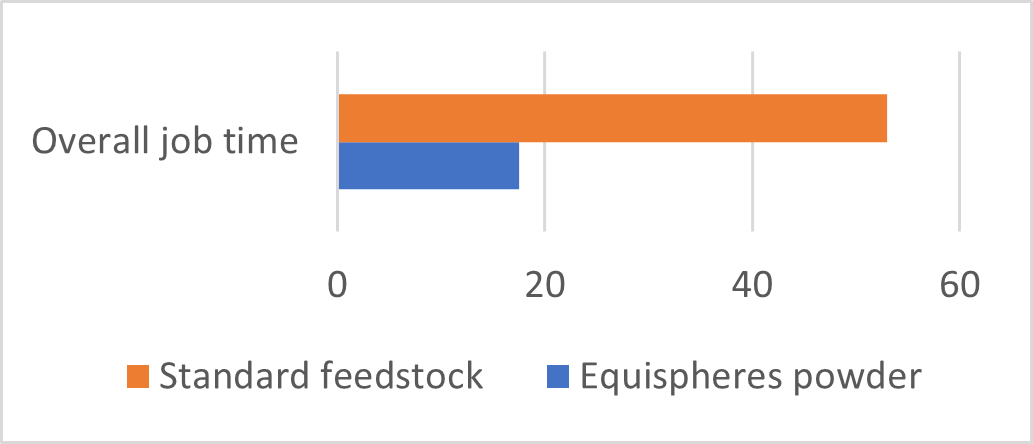
Outstanding part quality even at high build rates
The part manufactured by Aconity3D measures 162 x 126 x 110 mm (LxWxH). It includes integrated water and air channels for cooling. Even at high build rates, Equispheres powder achieved >99.5% relative density. The part’s mechanical properties are comparable to parts produced with standard process parameters.
Surface roughness was minimally higher (Ra=12-14 µm) and minimally reduced detail resolution was observed.
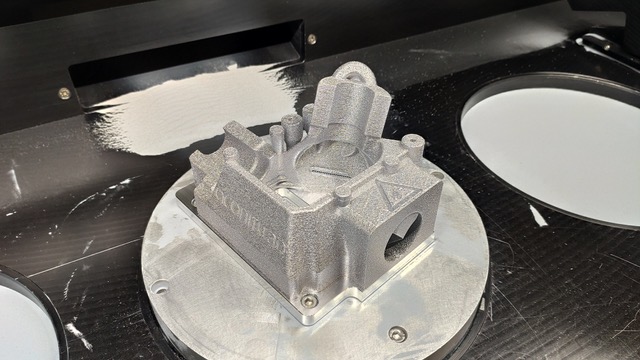
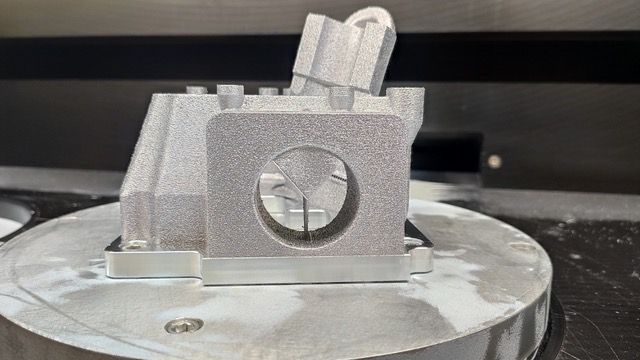
Why it matters
Printing time is a significant portion of part cost for 3D printing processes. For this part, the shorter build time reduced production costs by more than 50% compared with standard feedstock.
Part Costs | Standard feedstock | Equispheres Performance powder | Percentage decrease |
Cost per build | 2370 € (2,678 USD) | 986 € (1,114 USD) | 58% |
Cost per part | 592.5 € (669.48 USD) | 246.5 € (278.54 USD) | 58% |
Job cost constants: Personnel 100 € (113 USD); Preparation 80 € (90.41 USD)
Conversion 1€ = 1.13 USD, rate as of Jan. 24, 2022
Looking forward
Modern, high-precision powder bed fusion printers combined with high-performance powder specifically tailored for additive manufacturing can significantly increase the speed of part production and dramatically reduce costs.
Aconity3D was able to produce parts at 3 times standard production rates and reduce costs by more than 50%, making additive manufacturing competitive with traditional manufacturing techniques. Similar results have been achieved by other manufacturers using Equispheres’ feedstock.
For manufacturers in the automotive, aerospace and defense sectors, this demonstrates that significant increases in productivity are feasible. The time savings directly translate to per-part cost savings, making metal AM a practical solution for part-making in the manufacturing process.