The qualities that set Equispheres’ alloys apart from all other aluminum powders for 3D printing may not be visible to the naked eye, but there is a noticeable difference for those using the material. From powder handling through to the final product, the spherical nature of our particles and the lack of fines means the powder flows better, packs more densely and cleans-up more easily. The combination of these attributes profoundly affects printing speed and final part properties, but it also makes the material easier to work with.
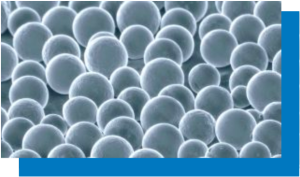
You can tell the difference as soon as you start to work with powders produced by Equispheres. I noticed it the very first time I printed with Equispheres’ material. I was a post-doc at McGill University in Montreal when I first used this aluminum powder.
In fact, I may have been one of the first people to put this material through its paces in laser powder bed fusion equipment. Equispheres was in the very early stages of development, but it was already evident the company had something special.
The first thing I noticed when I was building parts and doing materials characterizations was that the powder didn’t leave a mess in the printer. It doesn’t have tiny particles that stay suspended for longer lengths of time and stick all over the place.
There are two practical considerations that set Equispheres’ material apart: cleaning efficiency and ease of sieving. These factors may not be glamorous, but they matter a great deal when using a metal powder for day-to-day production.
We used a gravity-fed system on our 3D printer at the time. Other powders would create a tiny cloud of particles during the powder dosing process that would stick to the side walls and hard-to-reach areas. With Equispheres’ powder, we didn’t get that.
One of the other differences I noticed relates to binding in the sieve. With Equispheres’ powder, this didn’t happen, but I was getting binding with other powders in the same sieve. This phenomenon has an important impact on the process reliability when we put powder reuse and sieving efficiency into the equation.
For additive manufacturing firms, these are two practical considerations that set Equispheres’ material apart: cleaning efficiency and ease of sieving. These factors may not be glamorous, but they matter when using a metal powder for day-to-day production.
Years later, testing by McGill confirmed that Equispheres’ powders actually flow 2.5 times faster than competing powders.
Purpose-built for additive manufacturing
The best powders for metal additive manufacturing are those designed from the ground up for that purpose. From the beginning, Equispheres has used its materials technology to create powders with ideal properties for metal AM. These include:
- uniform size,
- sphericity,
- consistent microstructure,
- smoother surface, and
- thinner oxide layer
Round and smooth particles move more freely than irregularly shaped particles with microscopic fines (ø: 0.1–5µm). Powders with irregular shapes and fines tend to clump and prevent uniform layer deposition in the laser powder bed process due to inter-particle cohesion.
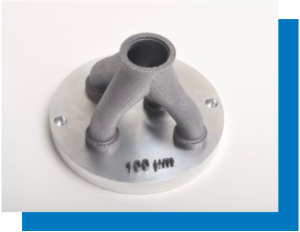
“Equispheres’ powder is spherical and free of agglomerates and fines, so it moves smoothly under the powder bed blade/roller at a variety of recoater speeds for much better spreadability.”
Irregular particles and fines interfere with packing density. Equispheres’ powders pack much more densely and uniformly than competing powders. They can produce denser parts with smoother as-built surfaces.
The result is simply a final product with a superior surface finish and better mechanical properties.
Equispheres’ powder melts and solidifies uniformly and predictably with minimum microporosity. The typical pore number density obtained with optimized parameters ranges between 3 to 6 pores per mm². This advantage allows us to have a wide processing window with consistent and superior mechanical properties.
The specifications for our material only reveal a part of the story. Those with hands-on experience in 3D printing metal parts will recognize how much this material changes the additive manufacturing process. It’s not just the positive effect on the end part. It’s the handling of the powder, the ease of cleaning, the process reliability, the thicker layers and the faster build speed.
Having worked with the powder for several years now, I have also been able to confirm some less obvious benefits through experimentation, like the powder’s tendency to absorb less moisture from the atmosphere and the stability of its properties when reused.
All these properties change the dynamics of the 3D printing process – for the better.