In the rapidly evolving world of metal additive manufacturing, laser powder bed fusion has a bit more history behind it than some of the newer techniques. L-PBF technologies are advancing by leaps and bounds but a few outdated myths about powder-based processes persist. I’ve tried to dispel a few of the common myths below.
Anyone in our field who has tried to push their standard parameter set to higher print speeds has probably experienced lower density, diminished mechanical properties and reduced surface quality. With older LPBF equipment and traditional metal powders, that is the likely result. But with the right tools and feedstock, faster build rates are easily achievable.
Where older, lower-powered lasers and first-generation powders could only reliably achieve quality results with 30 or (sometimes) 60-micron layers, newer equipment can operate at 120-micron layers with significantly higher build rates.
Myth: You can’t print quickly with aluminum
Many people think printing with aluminum is slow.
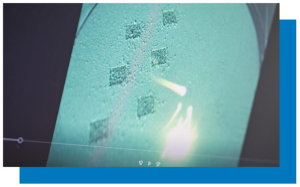
Honestly, with legacy powders not optimized for additive manufacturing, it WAS slow.
Now, however, if you have a powder that can give you a consistent, stable melt pool, you can increase the build rate without sacrificing part quality. Legacy powders spread inconsistently and they melt inconsistently. As operators increase power, speed and layer thickness, it creates instability in the process, which can impact part quality. Once you address the instability, by using purpose-built powder and newer equipment with tight process control, you can make good aluminum parts very quickly.
Myth: You need fines in the powder to make it pack well
It’s true that fines are desirable if you have a traditional powder-metallurgy process that involves tapping and packing the powder. But in powder bed fusion, we’re just spreading the powder.
Packing and spreading are not the same. For packing or tapping operations, you need a combination of small and large size particles to fill the gaps and increase packing density.
In powder bed fusion, what we need is very little cohesion among the particles. The lack of inter-particle cohesion allows the powder to flow better. In LPBF, the density of the powder bed is dictated by how well the powder flows.
I like to use the term “free flowing” to describe the behaviour of Equispheres’ powder… As the powder is spread onto the bed, the particles arrange themselves into a consistent dispersion because they flow freely and fall into a dense layer.
I like to use the term “free flowing” to describe the behaviour of Equispheres’ powder. Our particles are all similar-sized, very smooth spheres that flow exceptionally well, so they pack easily on the powder bed. As they are spread onto the bed, they arrange themselves into a consistent dispersion because they flow freely and fall into a dense layer.
Most powders for 3D printing – especially if they have a lot of fines, satellites, or odd-shaped, rough particles that prevent movement against each other – don’t achieve consistent packing density when spread over the powder bed.
Myth: Using more heat energy (higher powered lasers) leads to more stress in the part
Here’s a question I’ve been asked frequently: If you use a 1-kW laser printing at 120-micron layer thickness compared with a 400-watt laser at 30 microns, doesn’t it create more residual stress and warping because it’s putting so much heat into the part?
There are two problems with this thinking.
First, using a higher-powered laser and a faster build rate don’t necessarily result in more heat per unit of area. The actual energy density applied to the part might be less than with a lower-powered laser.
Second, energy density isn’t relevant here. Residual stress is more closely related to cooling rate and how you control other factors in the process. If you control parameters that affect cooling rate, you’re not necessarily going to build up more stresses in the part. If warping is a concern, application engineers can finesse parameters on a case-by-case basis.
One universal truth in additive manufacturing is that the shortest path to higher productivity is to reduce the number of layers you print and reduce the print time per layer.
Myth: Thicker layers will lead to a rougher surface
This one is not quite a myth; there is some truth to it. Thicker layers can result in an increase in surface roughness, but the misconception is HOW MUCH a quicker build rate will affect roughness. The effect on surface quality is not nearly as drastic as people think.
It varies for each project, but it is possible to achieve really good surface finish even at thicker layers. Before printing, establish the minimum and maximum surface roughness specifications, and then talk to an application engineer. Chances are you can increase build speed and layer thickness and still hit your roughness targets.
Aconity3D has documented some of its development work related to a part printed for the company’s own 3D printers. Printing with Equispheres’ powder at 120 micron layer thickness, Martin Buscher, Head of Testing Facilities at Aconity3D, says the mechanical properties are nearly identical to a standard parameter set they use at 50 micrometer layer thickness, while still achieving acceptable surface conditions.
In our experience, you can achieve excellent surface roughness at thicker layers and higher speeds if you have a powder that melts consistently and have predictable, reliable process control.
One universal truth in additive manufacturing is that the shortest path to higher productivity is to reduce the number of layers you print and reduce the print time per layer. Is there a trade-off between print speed and part quality? Not anymore. With the right powder and right equipment, you can have higher speeds and maintain part quality.
__
To understand how Equispheres powders contribute to faster build rates, read more here.